告别“野蛮生长期”。中国手机厂如何迎接供应链考验?
日期:2022-12-10 21:49:28 / 人气:300
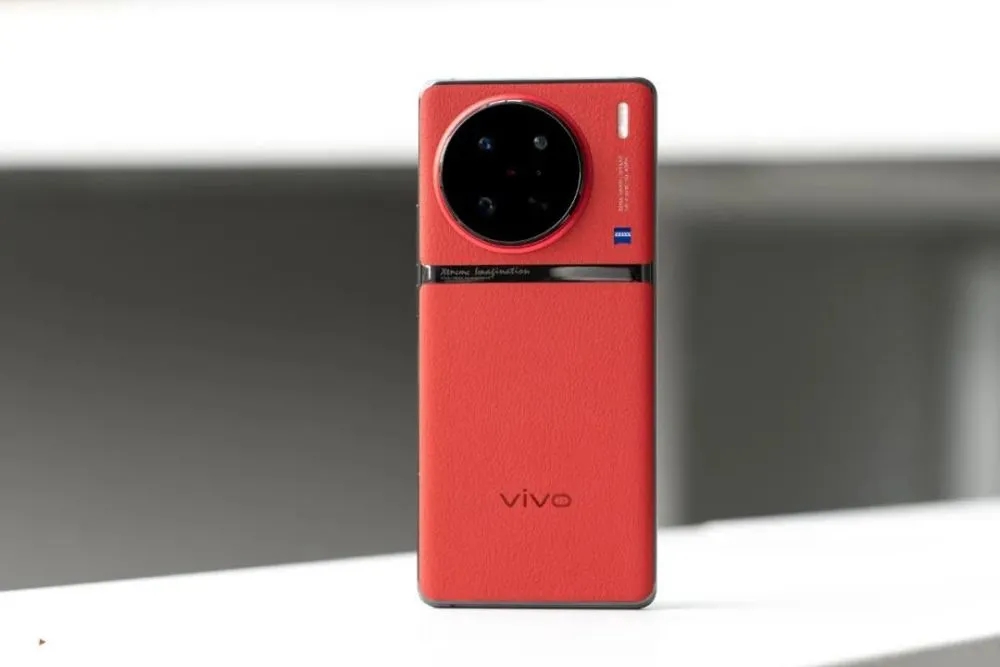
亨利·福特在1913年发明了工业装配线。第一次用流水线批量生产,而不是手工生产,从而以更低的成本打开了汽车工业革命的大门。100多年后的今天,在生产全球近70%智能手机的中国工厂,一场流水线上的智能化改造也在向前推进。
OPPO制造与品质事业部总裁郭晓聪近日在接受《第一财经日报》等记者采访时表示,从2020年开始,在内部实施“凤凰计划”,通过自我转型升级为智能制造。2017年至今,OPPO在设备上的投入已经接近20亿元。
除了OPPO,记者注意到,包括华为、荣耀、vivo、小米在内的中国头部手机厂商近年来也开始大举投资智能工厂。
在手机行业,技术迭代和市场环境的变化也在推动着传统工厂向智能工厂的转变。
在手机厂商看来,当全球手机市场逐渐从增量市场转向存量市场,智能手机行业发展逐渐告别“野蛮生长期”,过去粗放的工厂管理经验开始面临“失败危机”。在需求大变化的时代,面对不确定的环境,如何迎接供应链应变能力的大考验,成为当前手机厂商必须提前准备的挑战。
“过去的经验已经失败”
全球智能手机市场仍在低位运行。在刚刚结束的第三季度,全球智能手机市场出货量触及3亿部“警戒线”,同比下降12%,这是八年来最糟糕的季度数据。
Counterpoint的高级分析师哈默特·辛格·瓦利亚在评论全球手机市场的动态时说:各个地区日益增加的通货膨胀压力和对经济问题日益增长的担忧进一步削弱了消费者的情绪。该机构预测,智能手机市场的渠道库存已上升至8-10周,库存调整将再持续两个季度。
这给现在的手机制造带来了挑战。高增长环境下,过去一条手机生产线一个月换不了一次产品,手机销量好,直接增加了产量。但是市场一转,流水线上的产品一天换三次以上,SKU的复杂也增加了手机供应链的管理难度。
“2008年,OPPO每月只能生产20万部手机,2016年增加到200万部,2019年每月2000万部。产品数量也从一年十几个增加到现在的六七十个。”作为OPPO智能工厂的负责人,郭晓聪逐渐发现,产品种类越来越多,正在让生产流程变得复杂,曾经所依赖的“库存生产”体验正在失效,这一点在进入海外市场时更加明显。
“以前手机厂商的商业模式比较单一,基本只面向C端消费市场。但随着大规模进入海外市场,客户群以运营商为主,我们发现市场需求发生了很大变化。”郭晓聪告诉记者,运营商会要求厂商提供一定时间内的准确出货量预测,比如提前13周的订单。但过去OPPO主要依靠MTS make来备货,更多的是依靠对上一代产品的了解和性能来做产量预测。很难在短时间内对销售情况、版本和交付时间做出反应。
这直接导致了一个结果,工厂对销量的预测偏差很可能最终由OPPO自己“买单”。
实际上。随着出海步伐的加快,如何保证交付质量和交付水平的一致性成为中国手机厂商面临的最大挑战。在国外市场,尤其是运营商主导的欧洲市场,不同的国家、不同的运营商、不同的版本,对手机的定制和精准投放都有不同的要求。实现产品的高质量交付是极其困难的,因为一个“爆款”无法独霸天下,你也无法凭经验提交订单计划。另外,全球工厂的代工基地也不一样。
“在意识到问题后,OPPO决定从原来的MTS按库存生产模式转型为ATO的按订单生产模式。”郭晓聪说。
订单生产模式可以降低供应链波动带来的风险,但要再次推进生产模式推翻之前的流程并不容易。
一位国产手机厂负责人告诉记者,手机生产链涉及几十个环节。第一个环节是将整个计划转化为物料需求,并将生产与供应商的交货计划相匹配。供应商的物料到了工厂,还是需要和生产资源匹配,然后还是要处理内部仓储和外部物流运输的不确定性。模式的改变对手机厂商全链条的数字化统筹能力提出了更为严格的要求。
“我们产品的R&D周期大约是六个月。在产品定义阶段,需要和核心代理商、客户一起预测,并向各战区销售预测部(GTM)汇报。收集所有战区的需求,转化为计划,转化为长周期物资的准备申请。对于通用性强、周期长的物料,会在前期定型,而对于高度定制化的物料,会在生产前45天进行评估和预测。这样可以及时调整股票水位。”郭晓聪表示,这项涉及一体化供应链(ISC)、产融结合(IFS)、一体化销售管理(CRM)、一体化产品交付(IPD)的改革,内部称为“凤凰计划”。经过两年的实施,OPPO一台机器的制造成本下降了近40%。预计明年整个手机生产周期将从16天缩减到6天以内。
全球化下的供应链挑战
市场需求的变化成为倒逼中国手机厂商生产转型的导火索。但从时代发展的背景来看,中国手机厂商要想实现全球化布局,改造现有制造工厂势在必行。
受新一轮科技革命和跨国公司追求效率与安全平衡的影响,未来全球制造业和产业链供应链格局将朝着区域化、本地化、多元化和数字化方向调整和重塑。以苹果为例,其顶级供应商分布在全球600多个地点,而在制造基地布局上,除了中国,印度和越南也成为苹果拓展全球产业链布局的重点地区。
Counterpoint分析师伊万(Ivan)对《第一财经日报》表示,苹果代工公司长期以来在印度投资建设和培训工厂、生产线和生产人员。今年苹果在产品设计上也不断提高生产的模块化和维护的简化,海外工厂可以比以前更快的推出新产品。
过去几年,中国的手机企业也加快了全球工厂的布局。截至目前,小米在印度拥有7家制造工厂,在印度销售的手机99%都是在印度生产和组装的。印度中资手机企业协会秘书长杨树成此前告诉记者,除了小米,传音、OPPO、vivo等中国手机厂商也在2019年前后密集组织上游供应商考察印度市场。
根据印度蜂窝通信协会公布的数据,2014年,印度制造的手机仅占全球的3%。然而,在印度推广“印度制造”的第二年,印度制造的手机占全球的11%,并超越越南成为仅次于中国的第二大手机制造商。目前,大多数中国品牌已经从SKD(半零件组装)快速转变为CKD(全零件组装)以完成本土化。
但相比苹果选择富士康这样的EMS代工厂,中国手机企业更倾向于自建智能工厂,实现“制造标准”的统一。在业内人士看来,手机厂商与EMS代工厂的利益博弈由来已久,即使是强势的苹果也与供应链有摩擦。
郭晓聪表示,随着中国厂商在高端市场布局的深入,对品质闭环、R&D协同、供应链能力、全球布局等都有了更高的要求。“过去,R&D占据主导地位,工程难度被忽视。每个设备如何放置,应该预留多少空隙等。R&D以前不用考虑能不能自动化,现在自己的制造已经形成了R&D、供应商、售后服务等环节的闭环。一旦市场反映部分产品设计导致不良率较高,总部工厂可以迅速进行设计调整,然后在供应商体系中落地。同时,产品线立即跟进工程方案变更。”
一个例子来自印度智能工厂的设备调试。借助VR,工程师可以直接通过远程设备对折叠屏生产线进行指导和校准,无需来回奔波。关键流程量化后,OPPO可以在印度、巴基斯坦、埃及等全球十大制造中心实现数字化统一管理。
由于华为的全球通信设备制造背景在前期完成了智能工厂的推广,国内其他头部厂商近年来也在智能制造方面投入巨资,以期将其工艺认证能力和质量控制能力溢出到上游供应链,向更多国家输出统一的产品标准。
目前,北京昌平区小米智能工厂二期工程主体结构已经全面封顶。按照之前的计划。小米工厂将实现关键制造要素全流程100%数字化控制,在生产的各个环节使用AI、大数据、自然语言等20多项新技术。
去年11月,华为独立后的荣耀也在深圳坪山建设了超过10万平米的智能制造产业园。荣耀公司供应链管理部总监宋告诉记者,自建的智能工厂分别承载测试、量产、核心技术、技术孵化和智能制造能力建设,未来还将大量引进自动化设备作为高端零部件。这些制造能力也将在标准化后输出给供应链合作伙伴,从而更快完善全球供应链梳理。
“自建智能制造中心是典型的把R&D搬到后端,把制造搬到前端的工厂。R&D是把生产线上的工程师和工人请到R&D中心和新产品验证中心来攻克难题,因为制造非常清楚设计能否在生产线上实施,从而缩短整个制造过程的时间。”荣耀CEO赵明在此前的采访中告诉记者。
在这些手机厂商看来,手机形态的多样化和供应链的不确定性正迫使厂商在全球部署和交付上做出改变,通过制造工艺的标准化来实现量产的可靠性。在互联互通的全球经济体系中,虽然制造业面临的挑战骤然增加,但只有在标准化之后,才有可能在标准的基础上尝试信息化,并在信息化的基础上,通过数字化让数据流流动起来,赋能商业价值,最终实现手机工厂的智能化“转型”。
作者:风暴娱乐注册登录平台
新闻资讯 News
- 金秀贤事件深度调查:记者离世背...04-02
- 刘亦菲红毯封神:38岁的“神仙姐...04-02
- 王心凌演唱会风格大变,透视装引...04-02
- 江一燕新造型美炸啦!宽松西服...04-02
案例展示 Case
- 风暴娱乐活动06-22
- 风暴官网06-22
- 风暴娱乐iosapp下载06-22
- 风暴娱乐安卓app下载06-22
- 风暴平台06-09
- 风暴登录06-09